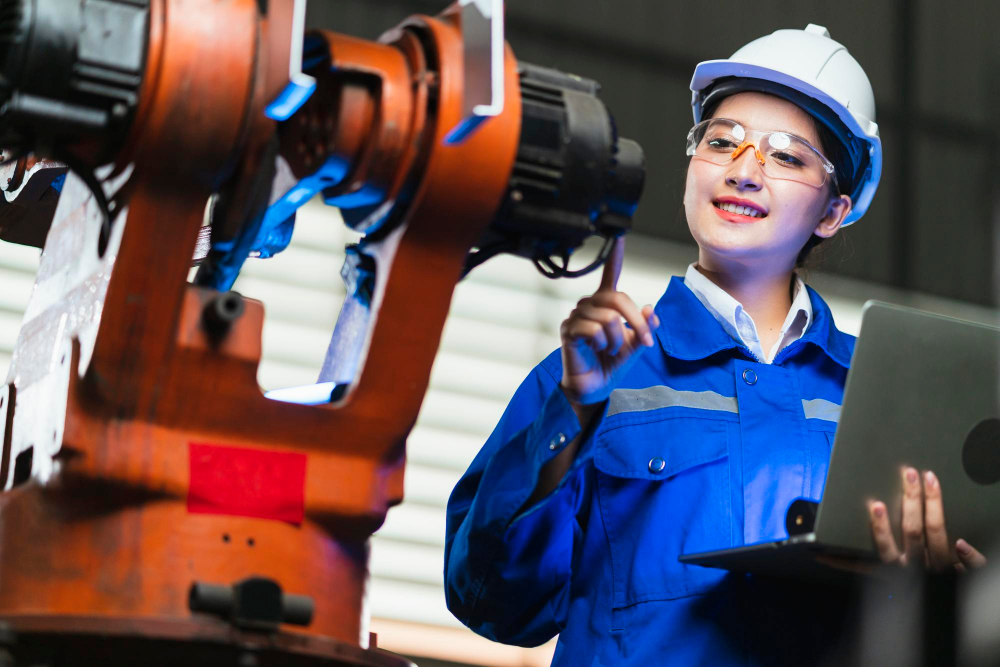
The manufacturing industry is undergoing a profound transformation, driven by advancements in technology and the integration of digital solutions. At the heart of this evolution are Manufacturing Execution Systems (MES) and Industry 4.0, two pivotal concepts reshaping how factories operate, innovate, and compete in the global market. In this blog, we will explore the future of manufacturing through the lens of MES and Industry 4.0, highlighting their significance, benefits, and the transformative impact they are having on the industry.
Understanding MES and Industry 4.0
Manufacturing Execution Systems (MES):
MES are comprehensive software systems that monitor, track, and control manufacturing processes in real-time. They act as a bridge between the shop floor and enterprise-level systems, providing critical data and insights that enable manufacturers to optimize production, improve quality, and enhance overall efficiency. MES helps in coordinating and managing everything from production schedules and inventory management to quality control and compliance with regulations.
Industry 4.0:
Often referred to as the Fourth Industrial Revolution, Industry 4.0 represents the integration of cyber-physical systems, the Internet of Things (IoT), and advanced data analytics into manufacturing. It’s characterized by the use of smart technologies that allow machines and systems to communicate with each other, making factories more autonomous, agile, and efficient. However, Industry 4.0 focuses on creating a connected and intelligent manufacturing environment where data-driven decision-making and automation are key components.
The Synergy Between MES and Industry 4.0
The combination of MES and Industry 4.0 is a game-changer for the manufacturing industry. While MES provides the foundation for monitoring and controlling manufacturing processes, Industry 4.0 adds a layer of intelligence and connectivity that enhances the capabilities of MES. Together, they enable manufacturers to achieve unprecedented levels of efficiency, flexibility, and quality.
- Real-Time Data and Insights: MES, when integrated with Industry 4.0 technologies, provides real-time data on every aspect of the manufacturing process. This includes machine performance, production output, and quality metrics. Manufacturers can use this data to make informed decisions quickly, leading to improved operational efficiency and reduced downtime.
- Enhanced Production Planning and Scheduling: The integration of MES with Industry 4.0 enables more precise production planning and scheduling. While smart systems can predict potential bottlenecks, optimize resource allocation, and adjust production schedules in real-time based on demand, machine availability, and other factors. This leads to a more agile and responsive manufacturing process.
- Improved Quality Control: Quality control is a critical aspect of manufacturing, and the combination of MES and Industry 4.0 significantly enhances this process. Advanced analytics and machine learning algorithms can identify defects, predict quality issues before they occur, and provide actionable insights to prevent future occurrences. This results in higher product quality and fewer recalls.
- Increased Automation: Industry 4.0 introduces a higher level of automation into manufacturing, with MES acting as the control center for these automated processes. Autonomous robots, smart machines, and automated guided vehicles (AGVs) can work together seamlessly, reducing the need for manual intervention and increasing production speed and accuracy.
- Predictive Maintenance: Predictive maintenance is another key benefit of integrating with Industry 4.0. By continuously monitoring the condition of equipment, manufacturers can predict when maintenance is needed, preventing unexpected breakdowns and minimizing downtime. This proactive approach extends the lifespan of machinery and reduces maintenance costs.
- Enhanced Supply Chain Visibility: With MES, manufacturers gain greater visibility into their supply chains. They can track the movement of materials and products in real-time, optimize inventory levels, and respond more effectively to disruptions. This increased transparency leads to a more efficient and resilient supply chain.
The Future Outlook
As the manufacturing industry continues to evolve, the role of MES and Industry 4.0 will become even more critical. Here’s what the future holds:
- Smart Factories: The concept of smart factories, where machines, systems, and humans collaborate seamlessly, will become more prevalent. Thus the Industry 4.0 will be the backbone of these factories, enabling fully automated and connected manufacturing environments.
- Personalization and Customization: Industry 4.0, combined with MES, will allow manufacturers to offer more personalized and customized products at scale. The ability to quickly adapt production processes to meet specific customer demands will become a key competitive advantage.
- Sustainability: Sustainability will be a major focus in the future of manufacturing. While Industry 4.0 MES reduces waste, optimizes energy use, and minimizes manufacturing’s environmental impact.
- Human-Machine Collaboration: While automation will increase, the future of manufacturing will still rely on human expertise. Human-machine collaboration improves with advanced interfaces, AR, and AI, simplifying control of complex systems.
Conclusion
The future of manufacturing is bright, with MES Solution leading the way in driving innovation and efficiency. Hence embracing these technologies keeps manufacturers competitive, enabling faster, cost-effective delivery of high-quality products in a changing market. MES and Industry 4.0 synergy transforms factories into intelligent, connected environments, driving the future of manufacturing excellence.